While
operating well drilling, the drilling
fluid centrifuge machinery is one of the central
equipment that is often used, its purpose is mainly used for separating fine
solid debris whose diameter size are 2-7 μm from the drilling fluid. By using the drilling fluid centrifuge to
remove solid debris, it can effectively well lubricate and protected the drill bit;
it also has a very important role of improving drilling bit speed. With the oil
drilling industry ways and the technologies are getting mature; the drilling
fluid centrifuge manufacturing technology has been greatly improved as well.
However, there are some inherent mechanical issues if not solved it will give
the operators many function issues.
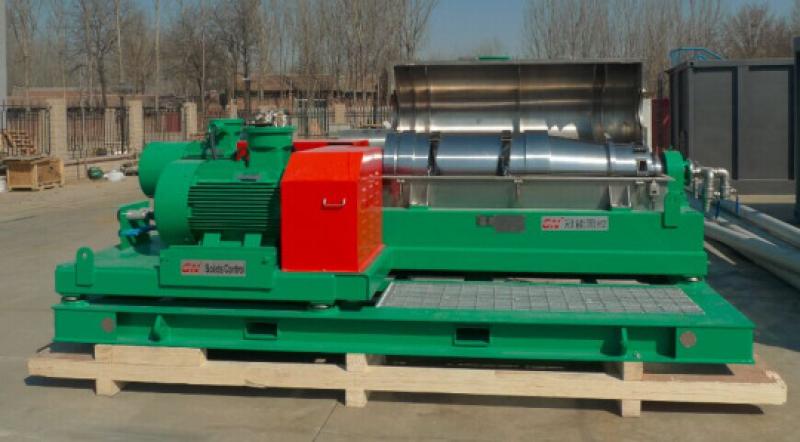
We as
manufacturer often have seen operators encounter issues below:
1. Bowl fault.
2. Consumable parts (inlet pipe, shockproof strip) problem.
3. Excessive vibration wile machine is currently working.
4. Outlet blocking by solids wish to remove from fluid.
5. Explosion-proof plug damage.
6. Centrifuge scroll damage.
7. Bearings failure while process of operation.
8. Drilling fluid centrifuge hoses damage.
We as
manufacturer suggest below if such issues operators encounter:
Operators
must understand that regular maintenance on the centrifuge such as regular
cleaning the inlet and outlet by filling water or diesel depends what kind of
fluid it needs process. It is also
crucial that add grease to the bearing parts to ensure proper lubrication.
Operators
needs regularly inspect often- damaged parts on the drilling fluid centrifuge,
such like hoses. In order to ensure the process in the use of these parts in
normal way this influences the production. Finally, electronic parts of the
centrifuge are working the best by running certain period of time frame (like
none-stop for hours). It needs, reduce the rapid turn on and off of the
centrifuge. If properly operate the centrifuge like mention above, then
operators will find out centrifuge failure rate will be greatly reduced during process
the drilling fluid.
Related Arciels: