Solve temperatures raise a
problem for decanter centrifuge
Decanter
centrifuge operation in proper RPM speed is the basis for normal
operation. Operation reach above normal
temperature and cannot come down is a major concern for decanter centrifuge
operation.
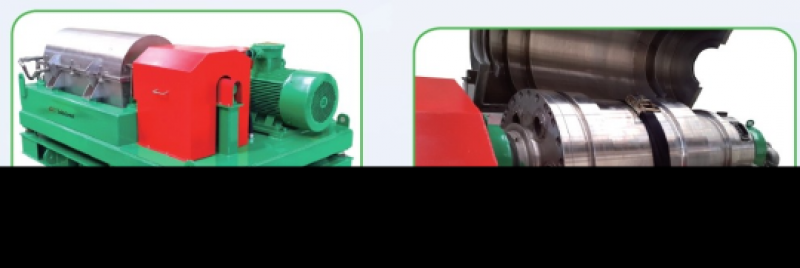
Normal
operation temperature for decanter centrifuge is around 104 degree F. It is normal when change the new oil from the
old, lubricants and turn the decanter centrifuge on, the temperature will be
raised up but later will be going down.
If the temperature does not go down, then there will be some place that needs
to be checked.
The
first ting need to check is the level of
oil and lubricants in the gearbox and bearing when the decanter centrifuge is
not on. Not enough oil and lubricants
will not grease the moving parts and gears in high speed operation will cause
grinding that lead to permanent damage.
The other side of problem if too much oil and lubricants will cause the
flow not flowing properly between gear
and parts. The air and oil mixing ratio
is not balanced will cause a temperature rise and not coming down as well.
Flush
the oil in the
gearbox of
Decanter centrifuge by turn the box upside down and drain all the
oil out. When the oil is completely out,
turn the filler hole to 10 o clock position and fill the gearbox oil. When filling the oil show the sign of
overflowing oil, it is filled with enough oil and should stop. Close the draining plug and do not topping
the gearbox oil.
Turn
the decanter centrifuge on and do the first temperature check. Then it needs to check very 15 minutes to get
the gearbox and bearing uprising temperature curve. Two hours later, after turn the decanter
centrifuge on, the temperature should reach to the top and start to show signs
to go down to 104 degree F.
If the temperature does not come down after 2
hours, stop the machine and open up the drain plug. Take the compressor connect with hose and
trigger and blow the air into the drain plug.
During the filling of the new gearbox oil, it might mix with air to
create air bubbles in the gear box.
Eliminate the air bubbles and turn the decanter centrifuge back on will
result the temperature comes down to normal operating temperature.
.��EKK