Since the new regulations for China oilfield
environment is issued, GN solids control has
provided over 25 sets of drilling waste management system for their water based
drilling fluids.
The main features of GN drilling cuttings treatment
system including:
1 Modular design: vertical
cuttings dryer, high G dryer, decanter centrifuge are all set on top of the
telescopic skid as a separate module, each module can be used separately when
the actual situation is required by the rigsite, and they can be used together
for best performance.
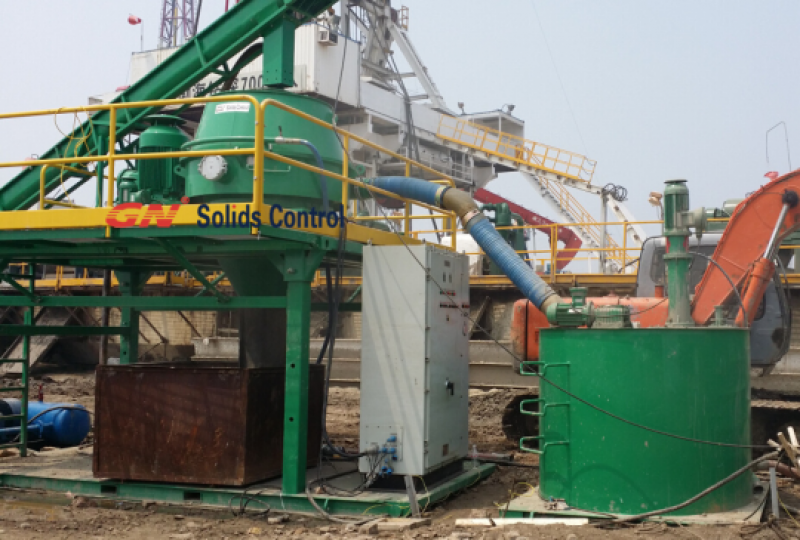
2 Less cost, good effect, the cuttings discharged from
the vertical cuttings dryer is dry as powder, which can be disposal directly or
used for construction industry without damage of the environment. Before using
GN drilling waste management equipments, the drilling company use the truck to
ship the drilling cuttings from the mud pit to a waste management factory, the
liquid waste spray out and they get a lot of complains from the farmers.
3 To recycle/reuse the clean fluids and less the
drilling cost. The working principal of GN drilling cuttings treatment system
is mechanical separation, without any chemicals additives. The clean fluids
discharged from
decanter centrifuge can be used for preparing the drilling fluids. Unlike
other supplier’s proposal, we do not add chemicals during the process, it will
not damage the configuration of the original drilling fluids, it can save a lot
of cost for the drilling fluids and less the waste treatment cost.
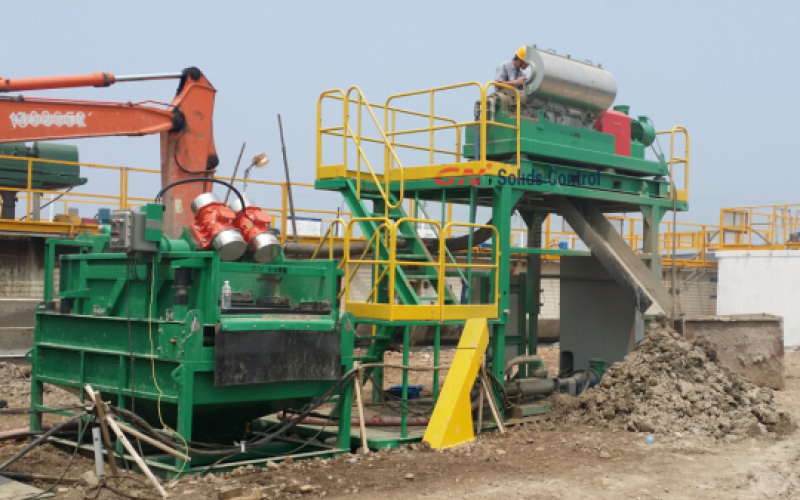
4 The high-G dryer is used to less the fine solids
content of the drilling fluids before feeding to the decanter centrifuge, the
unique design can make the centrifuge working longer time with less wear on the
screw impeller.
5 The drilling
waste management system for water based drilling fluids can be also used
for your oil based cuttings treatment, you do not have buy another unit , this
modular waste management system can be used for both of your applications.
/o:p�qpW"